The neck of an electric guitar is as important as the body and can affect the tone, appearance, and comfort of the instrument.
How the different parts of the electric guitar are manufactured is especially important to produce the object that your clients want.
What steps are involved to obtain a perfect electric guitar? Discover these in the following article!
Electric guitar neck and body manufacturing: how to select the right partner
There isn’t an ideal shape of an electric guitar neck or body, as it depends on the owner’s physical and aesthetic requirements as well as the sound they want to have. It is important, however, that each part of the guitar is managed properly to obtain a perfect object customized according to the client’s needs.
Wood is a difficult raw material to handle even with the right expertise, as it is alive and moves constantly. Moreover, each type of wood has different structural limits that you must consider when managing it.
To select expert electric guitar neck manufacturers, you must evaluate certain points. You should ensure that your wood maker performs specific steps during manufacturing before choosing it for your project.
5 crucial steps of electric guitar manufacturing
Here are some essential steps in electric guitar neck and body manufacturing that are needed to create a durable, resistant, and top-quality instrument.
Selection of the raw material
Manufacturing electric guitars starts from selecting the right logs. Their quality, in fact, influences the excellence of the final product, which must be solid and resistant. An expert manufacturer should perform strict quality controls over the raw materials, checking each piece manually and individually. Even if the external layers may appear perfect, the quality could be different inside.
Those pieces that conceal imperfections and defects should be discarded and reused to create other products or produce energy to fuel heating systems.
If this occurs—together with the exclusive use of FSC-certified timber—it means that the manufacturing company has a sustainable approach, which could make the difference to convince clients to buy your products.
Preparation of wood
Before manufacturing, the raw material must be prepared following a strict process to preserve wood density and prevent possible damage. The logs must be exposed to the air for two or three months to follow the natural drying process of timber and then put in special drying chambers that guarantee the correct degree of humidity before moving to production.
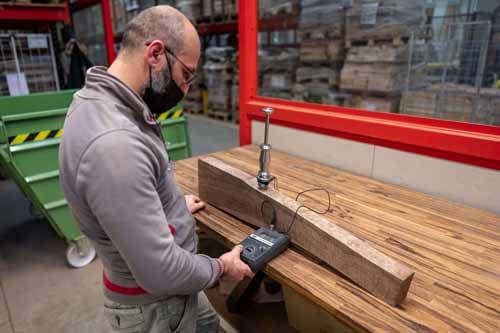
If the wood is too wet, volume may warp over time, causing functionality problems. The correct drying process ensures a stable ratio between volume and weight of the log, which is crucial to avoid discrepancies and breakage.
Production process
A reliable company should ensure:
- accuracy and precision
- cost-effectiveness
- high production capacity
- short lead time
In particular, the company you choose must guarantee the same quality for either a single product or for one million pieces, delivering them as scheduled. This can’t be taken for granted.
You should check if they work with both multinational corporations and small “sartorial” brands to be sure they can guarantee the same quality even at high production volumes. Producing wooden components in small lots and only when clients request them is also a great advantage, as this leads to greater efficiency and remarkable savings.
Moreover, most wood makers use multipurpose production equipment to manufacture their products, but it also means they can’t fit the purpose of manufacturing each specific product.
It would be important to select a manufacturer that can develop dedicated production lines for specific wooden components if necessary.
Customization
Your clients will expect to have the possibility of customizing their electric guitar with a wide range of finishing options, paintings, and varnishes as well as the possibility to create ergonomic shapes and designs to fit their requirements.
An international wood manufacturing company will be able to provide any kind of finish, including water-based lacquers, that have less of an impact on the environment compared with petroleum products.
The possibility of branding the electric guitar body can also be important.
A competent manufacturer will be able to create the logo on the body of the guitar with top-notch laser technology that different from silk-screening or hot stamping doesn’t need any ink or added chemical, being more eco-compatible.
Quality control
All parts of an electric guitar should be individually checked to ensure they respect all quality standards:
- dimensional and functional aspects
- milling accuracy
- morphological defects
An expert manufacturer uses sophisticated automatic systems of infrared video cameras and tailor-made artificial intelligence algorithms to ensure products that meet all customer specifications and expectations.
Only a technologically advanced wood manufacturing company that invests a lot of time and money to get the newest machinery and systems and is based on automation, interconnectivity, machine learning, and real-time data can provide top-quality and cost-effective wooden electric guitar necks and bodies.
Since 1937, Minelli S.p.A. has ensured perfection in the quality and design of each product manufactured, relying on the experience of our employees, the most innovative tools, and sustainable wood manufacturing processes.
We use only the latest generation of customized and made-for-purpose CNC machines that provide consistent dimensional and finishing results even at a very high production volume.
Moreover, thanks to our quality control systems with auto-learn function and the possibility to develop dedicated production lines to manufacture specific products, we can guarantee the highest-quality standards.
Il you have a project in mind, do not hesitate to contact us!